If just a few years ago the terms "artificial intelligence", "cloud computing" and "IoT" were not part of most people's vocabulary, today, this reality is different.
These are some of the concepts of industry 4.0, also dubbed the 4th Industrial Revolution, a phenomenon that is changing the way industry behaves and works.
With the intention of increasing the productivity and efficiency of the production stages, this revolution is an important milestone for everyone who works with technology. If you want to know more about industry 4.0 and its ramifications, follow this article.
What is industry 4.0?
The concept of industry 4.0 concerns the process of accelerating industrial production through the use of automation tools, such as artificial intelligence, robotics, the Internet of Things, among other solutions.
Its purpose is, of course, to provide more profitability for industrial operations, increasing the volume of production without increasing – and in some cases, even reducing – the cost of production.
It is worth remembering that industry 4.0, in itself, is not a technology, nor a methodology, but a set of concepts that encompass the use of new technologies to increase the volume and quality of production.
The main technologies of industry 4.0
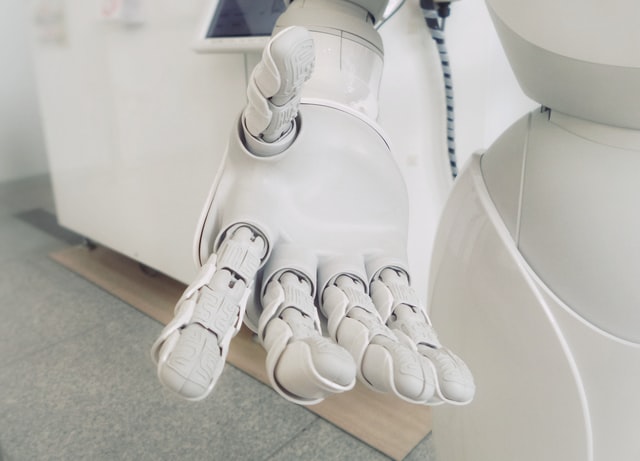
Without technological advancement, it is not possible to reap the benefits of industry 4.0. Thus, over the past few decades, hundreds of scientists and scholars have focused on the study of technology in order to design more efficient solutions to optimize production. Here are some of the most interesting technologies:
Artificial Intelligence
The use of Artificial Intelligence (AI) consists of the application of advanced analyses that make machines able to learn how to interpret events, perform trend analysis and automate decisions based on data.
With AI, you can make production costs lower without giving up performance, productivity, or production quality. The trend is that there will be an improvement of the intelligence applied in machines, making them even more cooperative in the future.
Internet of things
The Internet of Things – or IoT – is actually the connection of commonly used objects, such as machines or vehicles, for example, to the network. This connection allows these devices to communicate with each other and with the environment, creating an effective information exchange network and remote control.
Big Data
As you can imagine, all this technological advancement generates huge amounts of data to be analyzed, compiled and transformed into valuable insights for process improvement.
And that's where Big Data comes in.
Big Data is therefore the analysis and management of huge amounts of data. This technology is governed by 6 Cs, being:
- Content;
- Connection (to the industrial network, sensors and PLC);
- Community (sharing of information);
- Cloud (cloud/data on demand);
- Cyber (model and memory);
- Customization (customization and values).

Cybersecurity
Robust communication and connectivity systems are already an industry rule 4.0. In this way, identity management and equipment access software is increasingly intelligent, providing more reliable and secure communications.
Cloud computing or cloud computing
In cloud computing, systems are stored on shared servers connected to the Internet. Thus, they can be accessed from anywhere in the globe.
When we unite this concept with Industry 4.0, this means the possibility of breaking down old barriers of corporate servers, increasing the possibilities of connecting between different systems.
And the best; all of this can be done quickly and more efficiently than previous models.
Augmented reality
Such tools will be able to provide information in real time, with more agility and efficiency. The accuracy in delivering this data is critical to improving decision-making and, consequently, improving business processes.
Machine learning
With "machine learning", factories become smarter as equipment improves on their own.
In the service segment, for example, robots take the place of humans in customer service.
Of course, we are not talking about the sac of telephone companies; these are algorithms that learn over time and can meet customer needs more efficiently.
In addition, when we mention "robots", we refer to programs; a set of codes designed to fulfill specific functions.
Consequently, the quality of products and services increases significantly. After all, the learning of machines happens faster than that of humans.
Cobot
It is increasingly clear that the future of the market is collaborative. One aspect that proves this premise is the cobots. The term arises from the junction between collaborative and robot, resulting in a direct definition of the operation of these machines.
They serve to perform difficult, repetitive and effort-demanding activities. Their greatest advantage is that they can work side by side with humans, unlike many assembly line equipment, which often present risks to physical integrity.
In the case of cobots, they are equipped with sensors that block any movement that could harm a person. In addition, it allows any employee to temporarily control them to remove them from the path, for example.
Digital Twin
Called Digital Twins in some Brazilian industries, they consist of virtual models that simulate data collection to speed up and simplify preventive maintenance.
In practice, this technology aims to monitor industrial equipment and systems, identifying failures and avoiding minor or massive events — parts breaking or accidents with victims.
A great example of using this solution in industry 4.0 is aircraft engines manufactured by GE Aviation. They have several sensors that generate real-time information about their performance.
In this context, the Digital Twins monitor the conditions of the equipment — even at a distance — valuing its proper functioning and failure prevention and safety.
Importance of industry 4.0 in Brazil
According to 2018 data from the Brazilian Agency for Industrial Development (ABDI), less than 2% of all Brazilian organizations actually put into practice the concepts of industry 4.0.
According to the organization itself, this is a tremendous waste, as data indicate that Industry 4.0 could move $15 trillion over the next 15 years.
Studies from other institutions corroborate this scenario. A survey conducted by Accenture estimates that the application of IoT-related technologies has the potential to impact Brazil's GDP by US$39 billion by 2030.
Meanwhile, McKinsey research shows that by 2025, industry 4.0 can reduce equipment maintenance costs by up to 40%, reduce energy consumption by up to 20% and increase production efficiency by up to 25%.
Thus, Brazilian companies need, as soon as possible, to start applying the concepts of technological innovation in their operations, in order to reap fruits such as competitive advantage, creation of new markets and working positions and expansion of the production scale.
What are the benefits of industry 4.0?
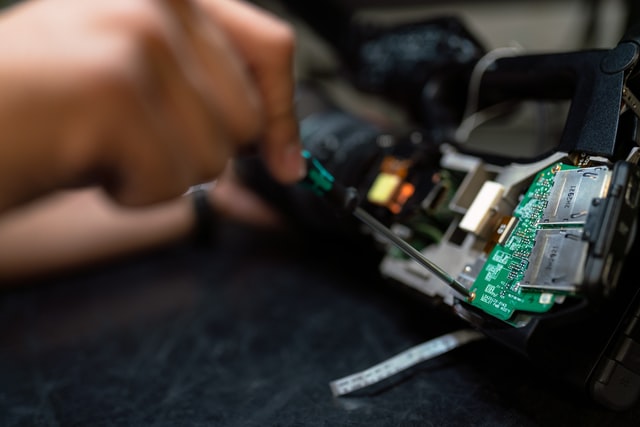
Companies only have to gain from the application of industry 4.0 concepts such as cloud computing, machine learning, the internet of things and big data analytics, for example.
Here are some of the key advantages of industry 4.0:
- More competitiveness;
- More efficiency in production;
- Reduction of errors caused by human action;
- Reduction of waste;
- Optimization of expenses;
- More assertiveness in decision making;
- More transparency in processes.
How can companies better prepare for industry 4.0?
Implementing industry 4.0 concepts is not a task that can be completed overnight. This process requires a great deal of planning and preparation, and that's what we'll talk about in the next few topics.
Here's how companies can prepare to implement industry 4.0 resources and reap their benefits:
Structure an initial project
Implement a pilot project before anything else. It will serve to measure implementation risks and costs, and give you a good idea of which processes need to be optimized or restructured.
Empower your professionals
Industry 4.0 is not intended to replace the human workforce, but to make it more skilled. Therefore, start by investing in the qualification of your employees, after all, they are the ones who will handle the new technologies.
Analyze the data
Your company produces a huge amount of data on a daily basis. Therefore, try to analyze and process this information in order to guide the decision-making process.
Key industry challenges 4.0
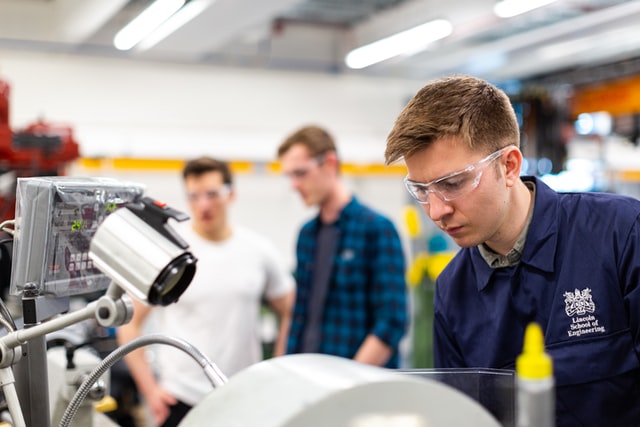
One of the main challenges related to the popularization of industry 4.0 is undoubtedly data security. Merging physical and digital environments requires more concern about cyber attacks as it makes storing information more vulnerable.
In addition, the training of employees is also a point of attention. Industry 4.0 technologies also need to be operated by skilled professionals to detect failures and optimize processes in conjunction with technologies.
And finally, industry 4.0 also faces challenges when it comes to the modularity of its solutions. Companies that want to step forward and start implementing technology solutions need to look for ways to work on interoperability of their operations, seeking continuous updates.
Conclusion
Industry 4.0 is a global trend, which is gaining more and more strength in Brazil. Its proposal is to accelerate innovation and increase the volume of production, also taking care of the quality of this process.
Nevertheless, implementing such innovations also does not come without a good dose of challenges. Professional training and information security are the main ones.
Companies that wish to be part of the innovation proposed by this that is considered the 4th Industrial Revolution should invest in the improvement of their professionals, in the creation of more robust security solutions and in the constant updating of their processes.
Did you like this content? So find out now how Master Certifications can help your business achieve Anatel Certification!
Find out even more about industry trends, check out our article on Smart Home!
Also learn about Digital Transformation in Companies and how to apply also in your business!